This is a continuation from a previously released article that can be found here.
Our previous discussion on the Keys to Efficient Preservation and Maintenance (P&M) covered how P&M impacts the various stages of a construction project through to the turnover and operational phases of the project. The article also covered how SiteSense® streamlines P&M for users on construction sites. However, accurate tracking of P&M of construction materials is also important from a managerial and legal perspective.
Tagged materials present an additional challenge for tracking P&M activities on a construction project. Tagged materials are components that have a unique tag number that defines the exact installation location of a piece of equipment, even when the materials themselves may be identical. For example, a power plant may have a series of identical pumps. However, each pump has a different tag number identifying its specific installation location in the plant, and each pump has a unique serial number associated with it. The drawings for the plant indicate where each pump is to be installed and will mention the pump’s tag number.
P&M is crucial during the entire life-cycle of the tagged material, before it is installed, during installation, during commissioning, and into operations, preservation is needed to ensure the part operates as expected. This can also become very important in the event of a warranty claim. Should the part fail, the supplier may only honor the warranty if the material has been properly preserved and maintained according to the manufacturer’s recommendations. In the event of a warranty claim, the equipment supplier may ask for the preservation and maintenance records. Failure to produce the records or missing P&M activities may result in the supplier not honoring the warranty.
Having the ability to track serial number and tag number relationships is not a nice-to-have; it is a requirement for maintaining traceability and P&M records throughout the project lifecycle.
In our original discussion, we covered how individual, on-site users track preservation and maintenance activities through SiteSense®. However, managers also need to be able to verify that the required preservation is taking place and coordinate preservation activities across the project. SiteSense® provides on-demand downloadable reports with important information at the finger tips of managers and supervisors when they need it most.
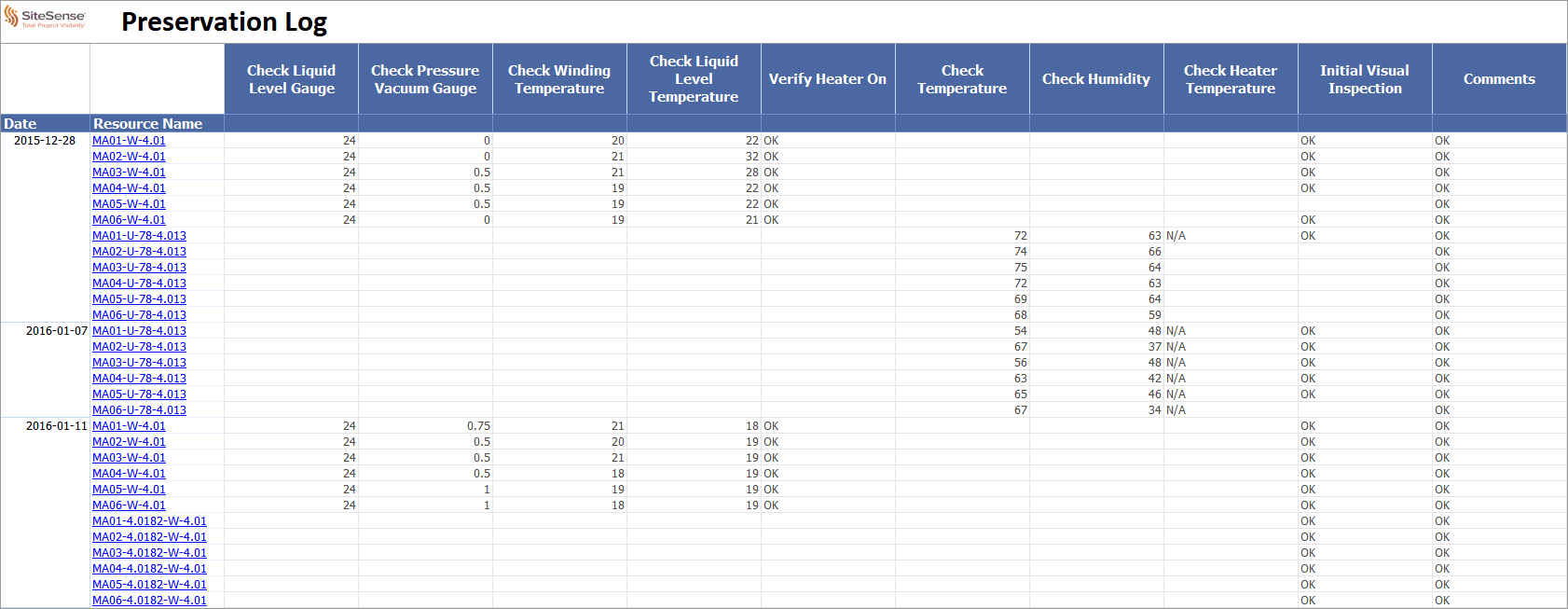
Figure 1: Preservation log sorted by date and part number
The report above shows information relating to P&M activities performed SiteSense® users creating an auditable trail for managers and supervisors. If a dispute should arise, managers have documented evidence to back up their claims which can lead to substantial cost savings for equipment replacement should parts be faulty during start-up.
Managers and foreman can also use SiteSense® to verify that the proper preservation is being done by their crews. They can also see a list of the upcoming required P&M activities to plan resources and ensure no P&M activities are missed.
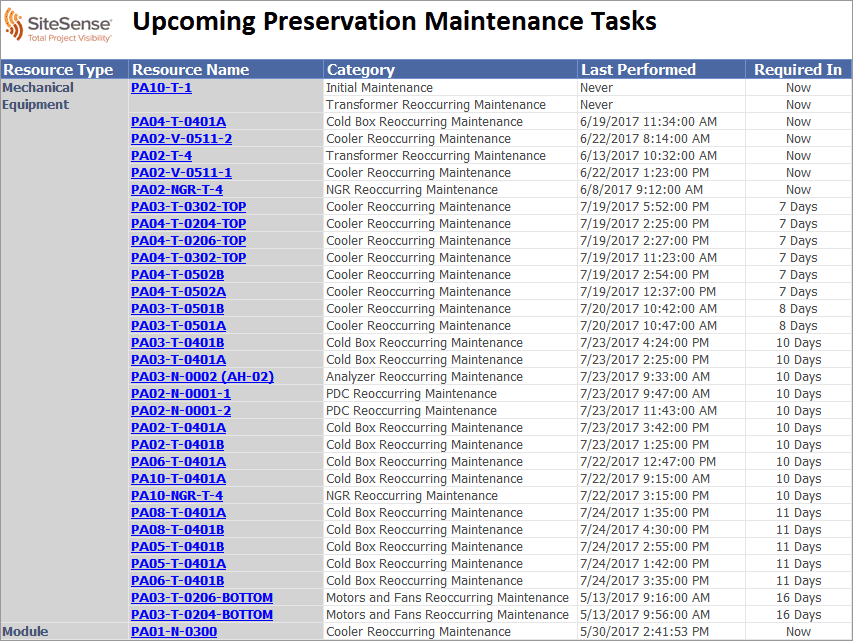
Figure 2: List of upcoming preservation tasks
From construction to commissioning, to operations, each of these steps involves the legal transfer of care, custody, and control and each group needs access to all the required records for tagged material in the plant to complete their respective tasks. Having the records automatically digitized and readily available on SiteSense® saves time and eliminates the risk of paper records being lost or accidentally destroyed.
With the increasing cost of equipment and its high technical content, using the right tools, to provide the right information, saves time and money. Even with the best of intentions, when activities are not documented, they have not legally happened. Should an incident occur, the fault can always be found with those who failed to document their work, even if they did follow the proper procedures. This idea can be summarized by a simple rule, “If you didn’t document it, it didn’t happen!!”.
SiteSense® provides the tools to avoid not only costly repairs and replacement but also empowers managers with the ability to verify that the P&M work they expect to be done, is in fact, being done.