Receiving and managing material for construction projects poses a unique set of challenges. Most procurement and accounting for major construction projects is performed offsite by centralized services using an Enterprise Resource Planning (ERP) system such as Oracle. ERP systems are powerful tools that allow for sharing of data across an organization. However, in construction, remote site locations and field personnel pose additional challenges for sharing and acquiring real-time, accurate information.
In this article, we are going to explore what a typical material receiving workflow looks like on a construction site, the pain points and how we can alleviate those pain points by integrating Oracle or any other ERP system with a field mobile material management system such as SiteSense®.
Below is a simplified receiving process for a construction project using an Oracle ERP system to handle procurement along with a manual process for receiving material on a construction site.
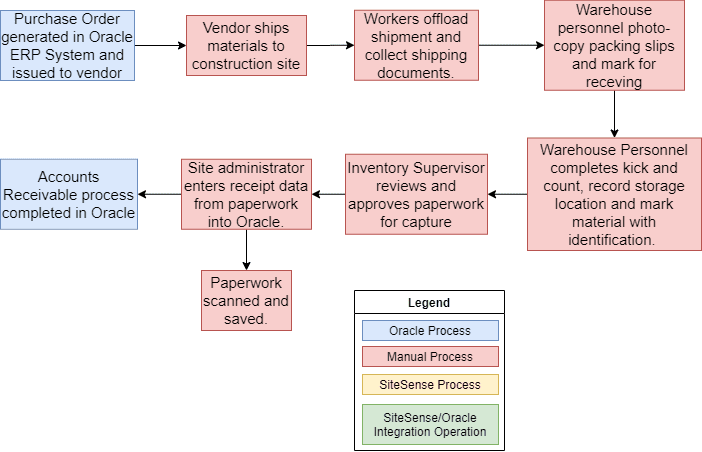
This process is functional but is very time consuming, lacks visibility and is error prone. Let’s examine all three issues and their impact.
Time-Consuming
The process relies on physical paperwork to relay information between team members. This can cause significant delays, often in the order of days or even weeks from when the material first arrives at site to when the receipt information is captured in the Oracle ERP system. Paperwork sits at each step until the responsible person has time to verify it, process it and move it to the next step. As the project ramps up and material shipments peak, this problem compounds, and can become crippling to the project as the workforce scrambles to find and process the highest priority materials.
Lacks Visibility
Until such time that the receipt has been captured in Oracle, it can be difficult to know which material has arrived or where it is in the receiving process. This leads to frustration and results in time consuming searches for both paperwork and the physical material. The significance of these delays are amplified when construction needs specific material or if receiving expedited material becomes high priority. Furthermore, the construction and scheduling teams may not become aware of any quality issues that arose from the kick and count that may impact the materials availability, giving these teams limited time to plan for contingencies.
Error Prone
As information is relayed with paperwork, there are significant opportunities for errors to be introduced. Warehouse personnel performing the kick and count have access to a limited set of information, often fostering incorrect assumptions about the material being received. The delay between the kick and count procedure and data capture into Oracle makes it difficult to clarify any concerns, and frequently results in additional trips to locate material and validate information. In the worst case, paperwork can be lost resulting in time wasted searching or re-doing the kick and count process.
Some project sites will use Excel based shipping logs or similar processes to try and track material. However, these methods have serious limitations and provide only limited information.
Streamlining the material receiving process using a field mobile materials management system such as SiteSense®, and integrating with an ERP system will allow for significant portions of the process to be automated. Integrating SiteSense® into the field significantly reduces both the delay and potential errors. Here’s what a high level receiving process, can look like when using SiteSense® integrated with an ERP system.
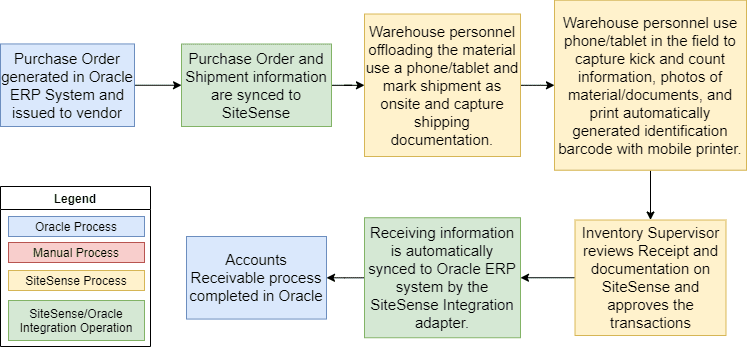
Time Savings
By automating the transfer of purchase order and shipment data from the Oracle system to SiteSense®, field personnel now have access to accurate and timely information in the field when they need it the most. Since data is captured live into tablets, the process eliminates duplicate handling of paperwork and secondary data entry as the SiteSense Integration Adapter automatically pushes the goods receipt data to the ERP system.
Visibility
Since each step in the process happens live within SiteSense®, there is no delay between the kick and count physical process, and the data captured in the system. All stakeholders have immediate access to all information providing an instant improvement in visibility. SiteSense® access is available to all users, field or home office via the SiteSense® web and mobile software applications. Providing this live access to all users, eliminates unnecessary emails and phone calls inquiring about material status.
SiteSense® includes a variety of dashboards and powerful search features for Inventory and Material Managers to, at glance, see the status of different Materials, Purchase Orders, Shipments, Receipts and Withdrawal Requests allowing them to effectively prioritize and manage Warehouse Personnel activities.
Errors
Due to the the number of touch points being reduced, the opportunities for errors are also reduced significantly. Additionally, since Part, Purchase Order and Shipment information are available to the Warehouse Personnel on their phones or tablets when completing the kick and count process in the field, Warehouse Personnel are less likely to make mistakes identifying material and matching line items.
SiteSense® also provides an intuitive platform which allows Warehouse personnel to easily capture pictures and associate it with Material and/or Documents. Tablets paired with mobile printers can be used to print material specific labels and barcodes. The pictures combined with accurate, easy to read labels make locating and identifying the material faster and more reliable.
In Conclusion
In this article, we looked at how integrating Oracle or any ERP system with SiteSense® can save time, improve visibility and reduce errors in the material receiving process. Similarly, integration with SiteSense® can be further extended to other construction processes, such as deficiencies, issuing to the field, work packaging and inventory anagement.
SiteSense® Integration Adapters are available for both the on-premise versions of the Oracle ERP system and cloud variations along with many other ERP systems. Contact Intelliwave today to get started. Visit www.intelliwavetechnologies.com for more information.